Kevlar, a material synonymous with protection and durability, has transcended its initial use in bulletproof vests to become a staple in a variety of safety gear, including biker apparel. This article delves into the remarkable journey of Kevlar, exploring its historical development, unique material properties, and its pivotal role in personal protective equipment. We'll also examine the innovative uses of Kevlar in biker safety, the meticulous processes behind its manufacturing, and the rigorous standards that ensure its quality. As we look to the future of protective fabrics, we'll consider emerging technologies, market trends, ethical implications, and real-world case studies that highlight Kevlar's impact on safety and protection.
Key Takeaways
- Kevlar's evolution from military use to civilian markets exemplifies its versatility and widespread acceptance as a protective material.
- The material's chemical composition and mechanical strength make it ideal for applications requiring resistance to impact, heat, and wear.
- Advancements in Kevlar's integration into personal protective equipment have significantly enhanced user comfort and wearability.
- In the realm of biker safety, Kevlar has been instrumental in reducing the severity of road rash injuries and improving overall rider protection.
- Sustainability and ethical considerations are becoming increasingly important in the production and disposal of Kevlar, influencing future innovations and applications.
Historical Development of Kevlar
Discovery and Early Applications
The genesis of Kevlar can be traced back to 1965 when Stephanie Kwolek, a chemist at DuPont, inadvertently created the first iteration of this super fiber during an experiment aimed at finding a lightweight yet strong fiber for car tires. The discovery was serendipitous, as the resultant fiber exhibited exceptional strength and stiffness, far surpassing expectations.
Kevlar's early applications were primarily industrial, including use in racing tires, owing to its high tensile strength-to-weight ratio. It wasn't long before the potential for personal protection was realized. The following list outlines the initial forays of Kevlar into various industries:
- Automotive: Enhancing the performance and safety of racing tires.
- Aerospace: Providing reinforcement for aircraft components.
- Maritime: Strengthening ropes and cables for ships.
Kevlar's transition from an industrial marvel to a staple in protective gear was propelled by its unique combination of lightweight, strength, and resistance to environmental degradation.
The material's adaptability and protective qualities soon caught the attention of the military and law enforcement agencies, setting the stage for Kevlar's evolution into a critical component of personal protective equipment.
Kevlar in Military and Law Enforcement
The adoption of Kevlar by military and law enforcement agencies marked a significant milestone in the history of personal protective equipment. Its unparalleled strength-to-weight ratio offered a new level of protection against ballistic threats, fundamentally changing the landscape of combat and tactical operations. The material's ability to absorb and disperse energy made it an ideal choice for body armor, providing soldiers and officers with the confidence to perform their duties in high-risk environments.
Kevlar's impact on military and law enforcement gear extends beyond bulletproof vests. Its use in helmets, gloves, and even vehicle armor plating has been instrumental in enhancing the safety and survivability of personnel in the line of duty.
The integration of Kevlar into protective gear has evolved over the years, with continuous improvements aimed at increasing comfort without compromising safety. The table below highlights some of the key advancements in Kevlar-based equipment for military and law enforcement use:
Generation | Improvement | Impact |
---|---|---|
1st Gen | Basic vests | Introduced the concept of wearable ballistic protection |
2nd Gen | Enhanced vests with trauma plates | Improved protection against higher caliber rounds |
3rd Gen | Modular systems with scalability | Allowed for customization based on mission requirements |
Current | Integration of smart fibers | Potential for real-time monitoring of wear and damage |
As Kevlar continues to be a critical component in protective gear, its development is closely aligned with the evolving needs of military and law enforcement personnel. The quest for lighter, more flexible, and even smarter materials remains at the forefront of research and development in the field.
Expansion into Civilian Markets
Following its success in military and law enforcement applications, Kevlar began to make its way into the civilian sector. The material's unique properties, such as high tensile strength and resistance to abrasion, made it an ideal candidate for a variety of consumer products. One of the most notable expansions was into the realm of personal safety and protective gear for civilians.
The integration of Kevlar into civilian markets can be seen across multiple industries. In sports, for instance, Kevlar has been used to reinforce equipment like skiing helmets and racing sails. The automotive industry has also utilized Kevlar for reinforcing tires and brake pads, enhancing vehicle safety and performance. However, it is perhaps in the area of motorcycle safety where Kevlar's impact has been most pronounced.
Motorcycle shorts have evolved with materials like Kevlar and ergonomic designs for safety and comfort. Winx Wheels offers innovative gear catering to diverse rider needs.
The table below illustrates the diverse applications of Kevlar in civilian markets:
Industry | Application | Benefit |
---|---|---|
Sports | Helmets, Sails | Durability, Lightweight |
Automotive | Tires, Brake Pads | Safety, Performance |
Motorcycle Gear | Jackets, Pants | Abrasion Resistance, Comfort |
Material Properties of Kevlar
Chemical Composition and Structure
Kevlar, a remarkable synthetic fiber, owes its exceptional strength and durability to its unique chemical composition and molecular structure. It is a polymer made from the monomer para-phenylenediamine and terephthaloyl chloride, which form aromatic polyamide chains. These long, rigid molecules are highly oriented with strong interchain hydrogen bonds, resulting in a material that is both lightweight and extraordinarily tough.
The structure of Kevlar can be further understood by examining its crystalline orientation and the way the fibers are spun. This orientation is crucial as it contributes to the fiber's high tensile strength, which is five times stronger than steel on an equal weight basis. The tightly packed molecules resist pulling forces very effectively, making Kevlar an ideal material for ballistic and stab-resistant applications.
Kevlar's high tensile strength and low weight make it an indispensable material in protective gear, offering a balance of protection and comfort that is hard to match with other materials.
The production process of Kevlar involves the formation of a liquid crystalline solution that can be spun into fibers. These fibers are then treated under tension to further align the molecules, enhancing the material's inherent strength. The resulting Kevlar fiber is not only strong but also has a high degree of thermal stability, maintaining its integrity in extreme temperatures.
Mechanical Strength and Durability
Kevlar's reputation as a material of choice for protective gear is largely due to its exceptional mechanical strength and durability. This synthetic fiber exhibits a high tensile strength-to-weight ratio, making it five times stronger than steel on an equal weight basis. The durability of Kevlar arises from its ability to absorb and dissipate energy, providing resistance against cuts, punctures, and abrasion.
The following table summarizes the mechanical properties of Kevlar compared to other common protective materials:
Material | Tensile Strength (MPa) | Elongation at Break (%) | Abrasion Resistance |
---|---|---|---|
Kevlar | 3620 | 3.3 | High |
Steel | 400-500 | 20-30 | Moderate |
Leather | 20-30 | 30-80 | Low |
Nylon | 75-100 | 18-45 | Moderate |
Kevlar's ability to withstand extreme conditions without compromising its integrity makes it an indispensable material in the realm of personal protective equipment.
When selecting protective gear, such as a motorcycle jacket, it is imperative to consider factors like abrasion resistance and material strength. These attributes directly influence the level of safety and protection offered, especially in high-risk situations. Kevlar's robustness not only ensures safety but also extends the lifespan of the gear, making it a cost-effective investment over time.
Thermal Resistance and Flexibility
Kevlar's unique molecular structure not only provides exceptional strength but also endows it with remarkable thermal resistance and flexibility. These properties make it an ideal material for a range of applications where heat exposure and movement are critical factors.
The thermal resistance of Kevlar allows it to withstand extreme temperatures without degrading, making it suitable for firefighting gear and aerospace applications. Its flexibility, on the other hand, ensures that protective equipment made from Kevlar does not restrict the wearer's movements, which is essential in many professional and recreational activities.
Kevlar's ability to maintain its integrity at high temperatures while remaining flexible under various conditions is a testament to its advanced material properties.
For motorcycle enthusiasts, the flexibility of Kevlar is particularly beneficial. It allows for the incorporation of the material into biker gear, providing enhanced protection without compromising on comfort. Jackets and pants reinforced with Kevlar not only offer resistance to abrasion but also ensure that the rider has full range of motion during rides.
- Thermal Resistance: Maintains performance in extreme heat
- Flexibility: Allows for full range of motion
- Durability: Resists wear and tear over time
- Safety: Offers protection in high-risk situations
Choosing a motorcycle jacket with superior protection features like reinforced padding and ventilation options for comfort and safety during rides is crucial for any rider. Kevlar's adaptability in various protective gear designs demonstrates its ongoing evolution and importance in safety equipment.
Kevlar in Personal Protective Equipment
Bulletproof Vests and Body Armor
The advent of Kevlar revolutionized the development of bulletproof vests and body armor, offering unprecedented levels of protection to law enforcement and military personnel. These vests are designed to absorb and disperse the energy of a bullet, reducing the likelihood of penetration and subsequent injury.
- Level IIA: Suitable for low-velocity bullets such as 9mm FMJ RN.
- Level II: Offers protection against higher velocity bullets like the .357 Magnum JSP.
- Level IIIA: Designed to stop .44 Magnum SJHP and lower caliber ammunition.
- Level III: Capable of withstanding rifle rounds such as 7.62mm FMJ.
- Level IV: The highest level of protection, effective against armor-piercing rifle rounds.
The design and manufacturing of these vests prioritize a balance between protection, weight, and comfort, ensuring that the wearer can remain agile and effective in the field.
Quality control is critical in the production of Kevlar vests and body armor. Manufacturers adhere to strict standards to ensure that each vest meets or exceeds performance requirements. The National Institute of Justice (NIJ) sets certification standards, and vests must undergo rigorous testing to verify their protective capabilities.
Helmets and Shields
The incorporation of Kevlar into helmets and shields has significantly enhanced the protective capabilities of these critical pieces of personal protective equipment. Helmets, in particular, have benefited from Kevlar's high tensile strength, which helps to distribute the force of impacts more effectively, thereby reducing the risk of head injuries.
Shields, on the other hand, have seen improvements in their ability to withstand penetration and blunt force trauma. The lightweight nature of Kevlar allows for increased mobility and endurance, especially in situations requiring prolonged use.
The strategic layering of Kevlar in helmets and shields is a testament to the material's versatility and its ability to provide superior protection without compromising on comfort or functionality.
The following table outlines the key benefits of Kevlar in helmets and shields:
Benefit | Description |
---|---|
Impact Resistance | Enhances the ability to absorb and disperse shock. |
Penetration Resistance | Provides resistance against sharp objects. |
Weight Reduction | Offers a lighter alternative to traditional materials. |
Durability | Maintains integrity and protection level over time. |
Advancements in Comfort and Wearability
The evolution of Kevlar in personal protective equipment has not only focused on enhancing safety but also on improving comfort and wearability for the end-users. Manufacturers have recognized that protective gear is more likely to be worn consistently if it does not impede movement or cause discomfort over extended periods.
Recent advancements have led to the development of gear that balances protection with flexibility and breathability. For instance, the integration of Kevlar with other materials has resulted in lighter, more pliable fabrics that still maintain a high level of protection. This has been particularly beneficial in the design of motorcycle apparel, where riders require both safety and comfort for long rides.
The strategic placement of Kevlar panels in high-movement areas, alongside stretchable fabrics, has greatly improved the ergonomic fit of protective clothing. This approach ensures that the gear conforms to the body's natural shape and movements, reducing the likelihood of chafing and discomfort.
- Enhanced breathability through ventilated designs
- Ergonomic cuts for better range of motion
- Multi-layered construction for improved impact absorption
- Use of moisture-wicking materials to keep the wearer dry
These improvements have been well-received by consumers, who now have access to protective gear that does not compromise on comfort. The Winx RideReady Moto Pants, for example, are a testament to this progress, offering riders a comfortable experience without skimping on safety features like CE-rated armor.
Innovation in Biker Safety Gear
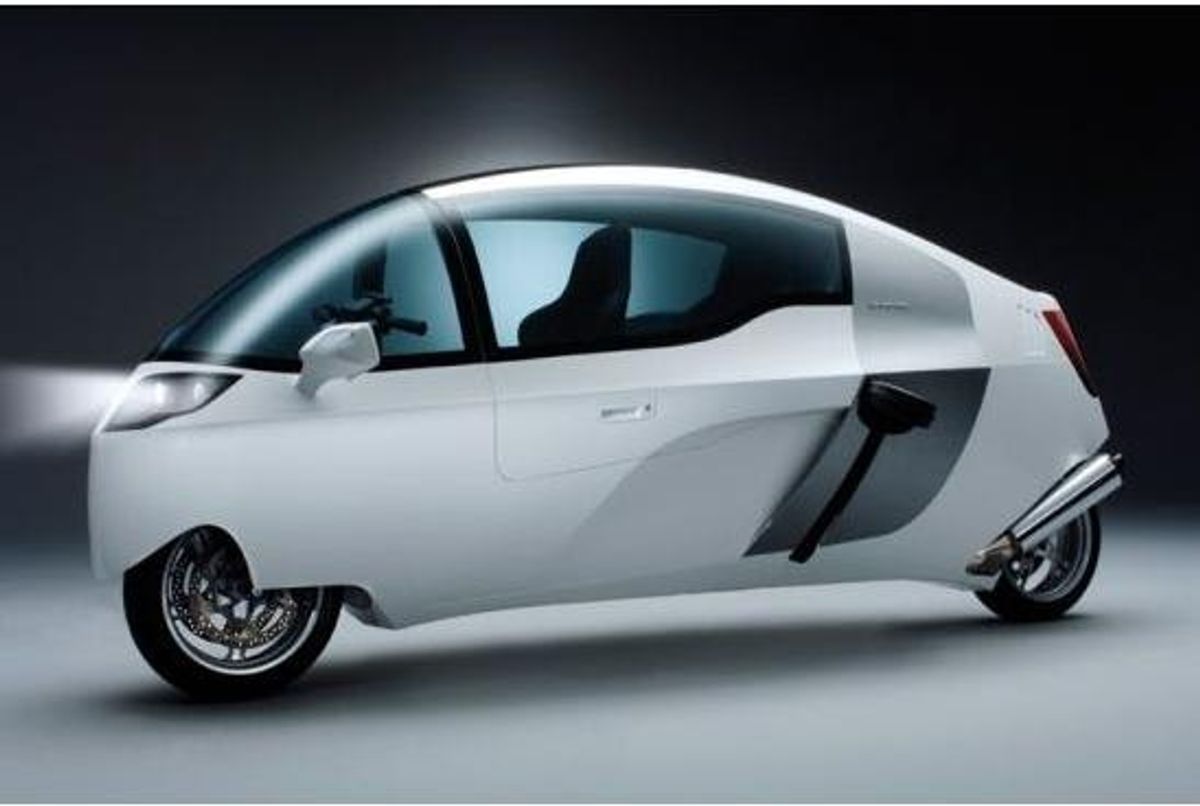
Integration of Kevlar in Motorcycle Apparel
The integration of Kevlar into motorcycle apparel has revolutionized the way riders protect themselves on the road. This high-strength material is now a staple in the construction of jackets, pants, and gloves, offering unmatched resistance to abrasion and tearing.
Motorcycle gear manufacturers have adopted Kevlar for its superior protective qualities, especially in high-impact areas. The strategic placement of Kevlar panels in garments is designed to provide maximum safety without compromising flexibility. Riders can now benefit from gear that not only protects but also enhances their riding experience.
The role of Kevlar in reducing road rash injuries is particularly significant. Its tough fibers create a barrier between the rider and the asphalt, greatly diminishing the severity of injuries in the event of a slide.
When selecting Kevlar-reinforced motorcycle apparel, it is crucial to research brands and read reviews to find the best protective gear. Advanced helmet technology not only offers safety but also comfort and connectivity, while visibility accessories further enhance safety. For those looking to personalize their ride, customizing the bike with graphics can add style without sacrificing protection.
Enhanced Protection in High-Impact Areas
The integration of Kevlar into biker safety gear has been a game-changer, particularly in the development of apparel designed to offer enhanced protection in high-impact areas. These areas, typically including the elbows, knees, and back, are most vulnerable during a crash. Manufacturers have responded by reinforcing these zones with Kevlar panels or inserts, which provide superior abrasion resistance without compromising the rider's mobility.
To illustrate the effectiveness of Kevlar in high-impact areas, consider the following table showing the comparative abrasion resistance of different materials in a controlled test environment:
Material | Abrasion Resistance (cycles to failure) |
---|---|
Kevlar | 1,200 |
Leather | 750 |
Denim | 50 |
Polyester | 25 |
Kevlar's high tensile strength and unique woven structure dissipate the force of impact, reducing the risk of injury in critical areas.
In addition to abrasion resistance, Kevlar-enhanced gear often incorporates padding or armor for added impact protection. This multi-layered approach ensures that riders are equipped with the best possible defense against the diverse risks encountered on the road. It's important for riders to gear up with helmets, armor jackets, and gloves for safety, and consider products like the Winx RideReady Moto Pants for both style and protection. Furthermore, upgrading to LED lights and reflective gear can significantly improve visibility, while carrying an emergency toolkit can be vital for on-the-go repairs.
The Role of Kevlar in Reducing Road Rash Injuries
Kevlar's unique properties have made it an indispensable material in the development of safety gear for motorcyclists. Road rash injuries, which occur when a rider slides across the pavement during an accident, can lead to severe skin abrasions and even permanent damage. The integration of Kevlar into biker apparel has significantly mitigated these injuries.
Motorcycle gear manufacturers have strategically reinforced high-impact areas such as elbows, knees, and shoulders with Kevlar panels. This targeted approach not only protects the skin but also reduces the likelihood of deep tissue damage.
- Enhanced abrasion resistance
- Reduced risk of lacerations and contusions
- Improved overall safety for riders
The incorporation of Kevlar into motorcycle gear has been a game-changer in terms of safety. Its ability to resist tearing and abrasion means that riders are far better protected against the common and often severe injuries associated with road accidents.
Continued research and development in the field of protective fabrics promise further advancements in the efficacy of Kevlar-based gear. As the material evolves, so too does the potential for reducing the severity of road rash injuries, making motorcycling a safer passion for enthusiasts around the world.
Manufacturing Processes and Quality Control
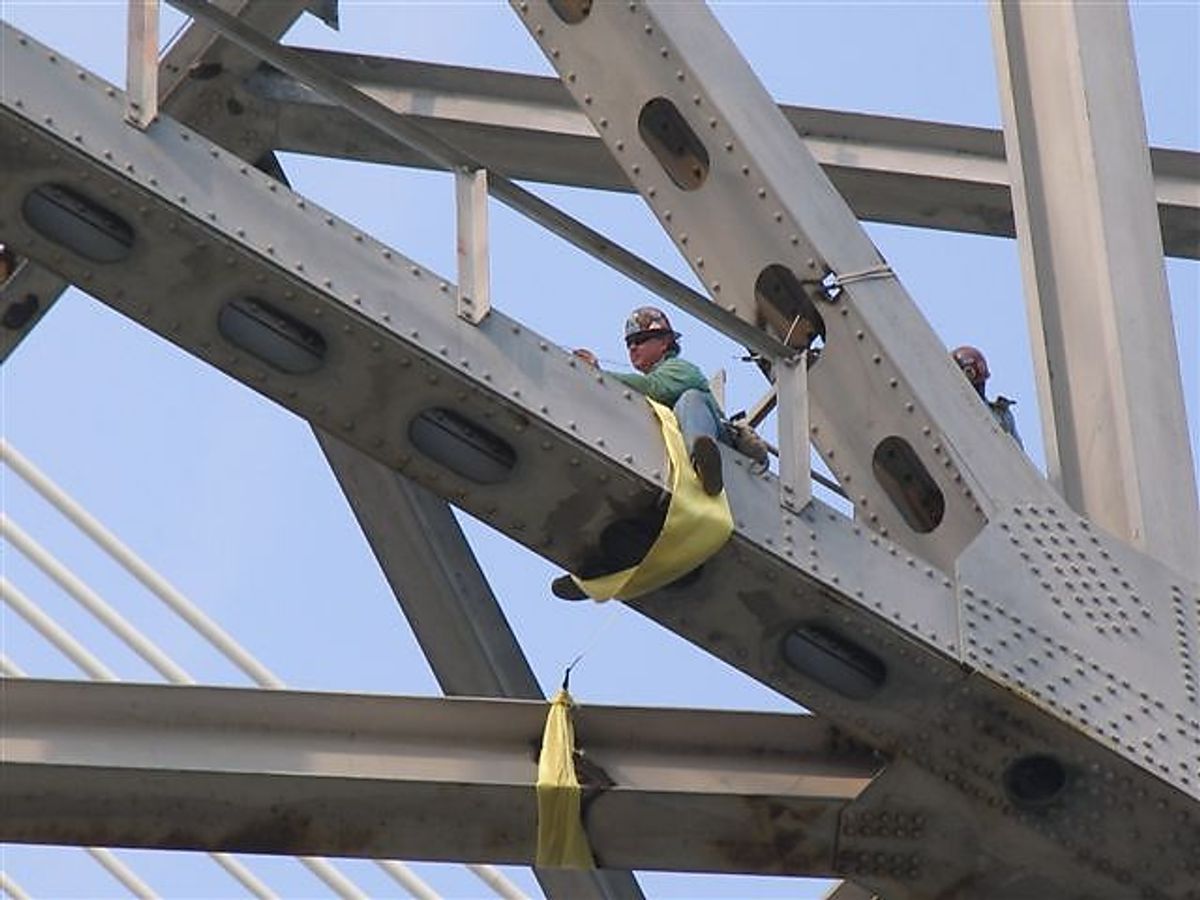
Weaving Techniques for Kevlar Fabrics
The manufacturing of Kevlar fabrics involves specialized weaving techniques that ensure the material's high tensile strength and durability. These techniques vary depending on the intended use of the fabric, with some common methods including plain, twill, and satin weaves. Each technique affects the fabric's properties, such as flexibility and resistance to abrasion.
- Plain weave is the simplest and most common technique, characterized by its checkerboard pattern. It offers a balance between strength and flexibility.
- Twill weave creates a diagonal ribbing pattern, which enhances the fabric's resistance to tears and punctures.
- Satin weave is less common due to its complexity but provides a smooth surface and greater flexibility, which is beneficial for specific applications.
The choice of weaving technique is crucial in tailoring the performance characteristics of Kevlar fabrics to specific protective gear requirements. Manufacturers must consider the end-use scenarios to optimize the material's protective qualities while maintaining comfort for the wearer.
Quality Assurance in Protective Gear Production
The production of protective gear, particularly those incorporating Kevlar, is governed by stringent quality assurance protocols. These protocols ensure that each product not only meets the required safety standards but also provides the necessary comfort and fit for the end-user. Manufacturers employ a variety of tests to assess the performance of protective gear under different conditions.
- Material Inspection: Raw materials are scrutinized for any defects or inconsistencies that could compromise the integrity of the final product.
- Design Evaluation: Prototypes are tested to ensure they conform to design specifications and provide the intended level of protection.
- Durability Testing: Finished products undergo rigorous wear-and-tear simulations to evaluate their longevity and resistance to various stressors.
- Safety Verification: Gear is subjected to impact and penetration tests to verify its protective capabilities.
Ensuring the highest quality in protective gear production is not just about meeting standards; it's about safeguarding lives. Manufacturers must balance the need for robust protection with the wearer's requirement for comfort and mobility.
The integration of features such as European CE-approved armor, abrasion-resistant materials, and reflective elements is a testament to the industry's commitment to safety. When selecting riding pants or other motorcycle apparel, it is essential to consider not only the material and protective features but also how well the item fits. A proper fit is crucial for both safety and comfort, allowing riders to focus on the road without distraction.
Sustainability Considerations in Kevlar Manufacturing
The manufacturing of Kevlar, like many industrial processes, presents various sustainability challenges. The production of this high-strength material requires significant energy input and involves the use of solvents and other chemicals that can be harmful to the environment if not managed properly.
- Energy Consumption: The synthesis of Kevlar's aramid fibers is energy-intensive, necessitating a reevaluation of energy sources and efficiency measures.
- Chemical Use: The process involves hazardous materials, which must be handled with care to prevent environmental contamination.
- Waste Management: Manufacturers are tasked with the proper disposal or recycling of production waste to minimize ecological impact.
- Lifecycle Analysis: Assessing the environmental footprint of Kevlar products throughout their lifecycle is crucial for identifying areas for improvement.
Embracing a circular economy model, where materials are reused and recycled, is becoming increasingly important in the Kevlar industry. Efforts to reduce waste and incorporate eco-friendly practices are essential steps towards sustainability.
In response to these challenges, manufacturers are exploring innovative approaches to reduce the environmental impact of Kevlar production. This includes the development of new recycling techniques and the search for alternative, greener solvents. As the industry progresses, the adoption of sustainable practices will not only benefit the environment but also respond to the growing consumer demand for eco-conscious products.
Regulatory Standards and Certification
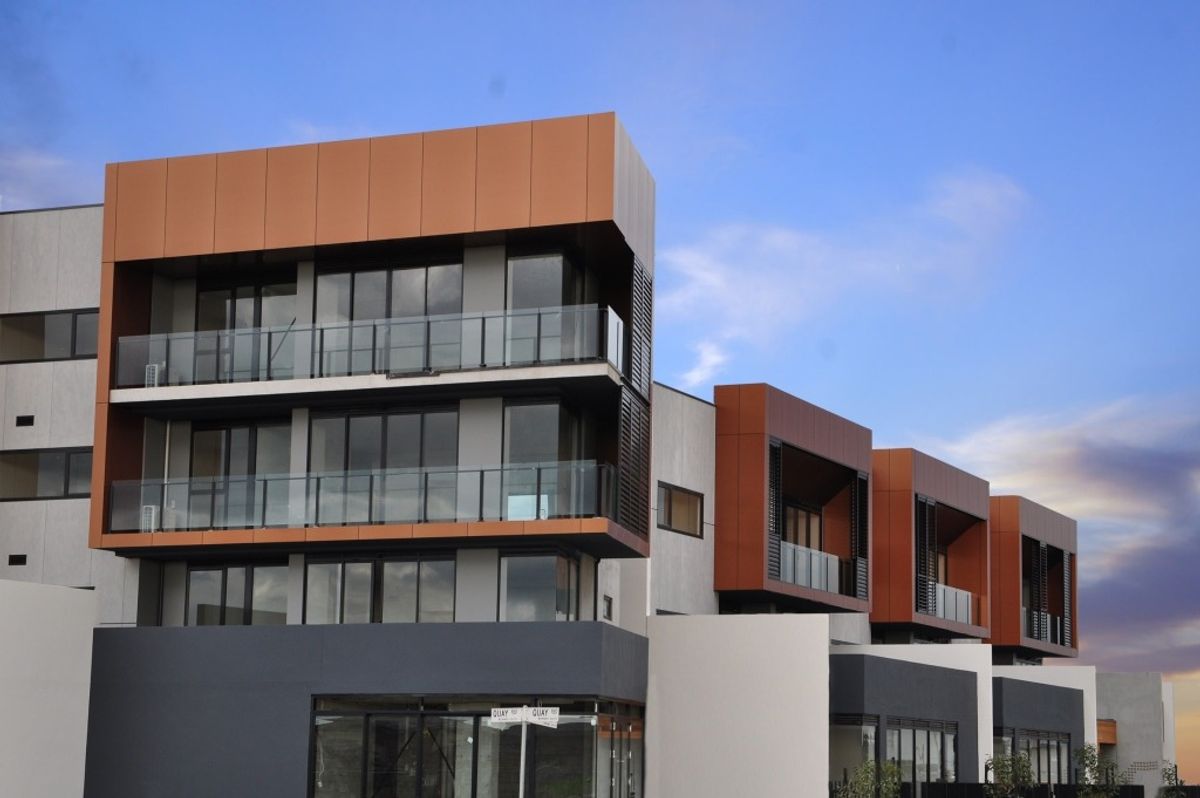
National and International Safety Standards
The establishment of safety standards for Kevlar-based products is a critical aspect of ensuring the protection they offer is reliable and consistent. National and international bodies have developed a series of benchmarks that manufacturers must meet to certify their products as safe for use. These standards are not static; they evolve to reflect technological advancements and emerging threats.
In the United States, the National Institute of Justice (NIJ) sets the standards for body armor. The NIJ Standard-0101.06, for instance, outlines the performance requirements for ballistic resistance of personal body armor. Similarly, the European Union has the EN 388 standard, which addresses the resistance of protective gloves to mechanical risks, including abrasion, blade cuts, tearing, and puncture.
The harmonization of standards across borders is essential to ensure that protective gear meets a universally accepted level of safety and efficacy. This global approach facilitates the trade of protective equipment and helps consumers make informed decisions based on recognized certifications.
Internationally, the International Organization for Standardization (ISO) plays a significant role. ISO 14116, for example, specifies the requirements and test methods for limited flame spread properties of materials, products, and clothing. To illustrate the scope of these standards, a brief table is provided below:
Standard | Description | Applicable Products |
---|---|---|
NIJ Standard-0101.06 | Ballistic resistance for body armor | Bulletproof vests, helmets |
EN 388 | Resistance to mechanical risks | Protective gloves |
ISO 14116 | Limited flame spread properties | Protective clothing, materials |
These standards are not only vital for consumer safety but also for legal compliance. Manufacturers must rigorously test their products to these standards to ensure they are fit for the market. Failure to comply can result in legal repercussions and a loss of consumer trust.
Testing Protocols for Kevlar-Based Products
The rigorous testing protocols for Kevlar-based products are crucial in ensuring their reliability and safety. Manufacturers and certification bodies employ a variety of tests to simulate real-world conditions and assess the performance of protective gear. These tests include ballistic resistance, abrasion resistance, tensile strength, and flexibility, among others.
- Ballistic Resistance: This test measures the material's ability to stop bullets and shrapnel. It is conducted using different calibers and ammunition types to ensure a comprehensive assessment.
- Abrasion Resistance: Essential for motorcycle gear, this test evaluates how well the material withstands wear and tear from rough surfaces.
- Tensile Strength: This determines the maximum load Kevlar fibers can support before breaking.
- Flexibility: Important for user comfort, this test checks the material's ability to bend and move without compromising its integrity.
The ultimate goal of these testing protocols is to guarantee that Kevlar-based products meet or exceed the expectations for safety and performance in their intended applications.
The results from these tests inform improvements in product design and are often used to validate compliance with national and international safety standards. For instance, motorcycle gear includes protective armor with CE certification for safety, adjustability, and ventilation. Weatherproof riding jackets use waterproof materials and ventilation for comfort in various conditions.
Certification Processes for Protective Gear
The certification process for protective gear, particularly those incorporating Kevlar, is a critical step in ensuring the safety and reliability of the products. Manufacturers must adhere to stringent testing protocols to meet national and international safety standards. This involves a series of assessments that evaluate the gear's resistance to impact, abrasion, and penetration.
The certification process not only validates the protective qualities of the gear but also ensures that the product meets the ergonomic and environmental standards required for consumer safety and comfort.
Certification bodies often require documentation and physical samples for testing. Once a product passes all required tests, it is awarded a certification mark, which serves as a symbol of quality and compliance. Consumers are advised to Choose high-quality gear with proper fit, certifications, and weather considerations for maximum protection and comfort while riding. Helmets, in particular, are essential for safety and offer additional features for an enhanced riding experience.
The Future of Kevlar and Protective Fabrics
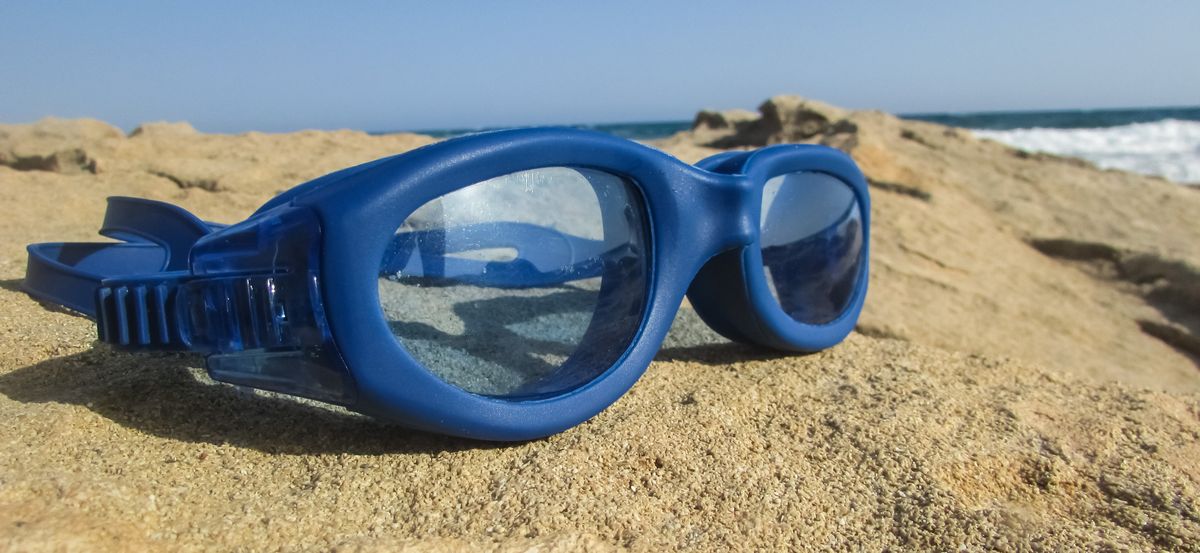
Emerging Technologies in Synthetic Fibers
The landscape of synthetic fibers is rapidly evolving, with new technologies enhancing the capabilities of materials like Kevlar. Innovations in polymer science and nanotechnology are leading to fibers with unprecedented strength-to-weight ratios and multifunctional properties. These advancements are not only improving the protective qualities of fabrics but also their adaptability to various applications.
One significant area of research is the development of hybrid materials that combine Kevlar with other high-performance fibers. This synergy aims to exploit the unique benefits of each component, resulting in composite materials that offer a balance of toughness, flexibility, and lightness.
- Graphene Integration: Adding graphene to Kevlar can increase its strength and introduce electrical conductivity.
- Nanotube Reinforcement: Carbon nanotubes can enhance the mechanical properties of Kevlar, making it even more resistant to impacts.
- Bio-based Polymers: Research into renewable polymers seeks to combine environmental sustainability with high performance.
The integration of smart technologies is also a key trend, with fibers being engineered to change properties in response to environmental stimuli, such as temperature or pressure. This could lead to protective gear that adapts in real-time to the conditions it encounters, offering dynamic protection.
As these technologies mature, they promise to open up new possibilities for protective fabrics, extending their use beyond traditional applications and into sectors like aerospace, automotive, and even consumer electronics.
Potential Applications Beyond Protective Clothing
While Kevlar is synonymous with protective clothing, its unique properties have paved the way for a multitude of applications beyond safety gear. The high tensile strength and thermal stability of Kevlar make it an ideal candidate for a variety of industrial and consumer products.
Kevlar's versatility extends to sectors such as aerospace and automotive, where it is used to reinforce tires, brake pads, and various composite materials. Its lightweight nature contributes significantly to fuel efficiency and performance enhancements.
In the realm of consumer electronics, Kevlar finds a place in the construction of robust, yet lightweight, casings for smartphones and laptops. The material's durability ensures protection against drops and impacts, while not adding significant bulk to the devices. Additionally, the fiber's excellent vibration damping properties are exploited in high-quality audio equipment, such as headphones and speakers, to improve sound clarity.
The sports industry also benefits from Kevlar's attributes, incorporating the fiber into equipment like racing sails, fishing lines, and high-performance ropes. These applications take advantage of Kevlar's resistance to stretching and abrasion, ensuring reliability and longevity under extreme conditions.
Challenges and Opportunities for Material Innovation
The evolution of Kevlar and similar protective fabrics is marked by a continuous interplay between challenges and opportunities. On one hand, the quest for enhanced performance and versatility in protective gear drives innovation. On the other, the inherent limitations of current materials and manufacturing processes present significant hurdles.
Material innovation in the realm of protective fabrics like Kevlar is not just about improving existing qualities; it's also about discovering new functionalities. For instance, the integration of smart technologies that can monitor the condition of the material or the health status of the wearer is a burgeoning field. However, such advancements must navigate the complex landscape of cost, manufacturability, and user acceptance.
The development of next-generation protective fabrics will likely focus on multi-functional capabilities, such as self-healing properties or the ability to adapt to different environmental conditions.
While the potential for Kevlar to evolve is vast, it is crucial to balance the pursuit of innovation with the practicalities of production and the realities of market demand. The following list outlines some of the key challenges and opportunities facing material innovation in protective fabrics:
- Challenge: Balancing material strength with flexibility and comfort.
- Opportunity: Incorporating nanotechnology to enhance fiber properties.
- Challenge: Ensuring sustainability in production and end-of-life disposal.
- Opportunity: Developing bio-based alternatives to synthetic fibers.
- Challenge: Overcoming high production costs to make advanced gear accessible.
- Opportunity: Leveraging economies of scale as demand for high-performance gear increases.
Case Studies: Kevlar in Action
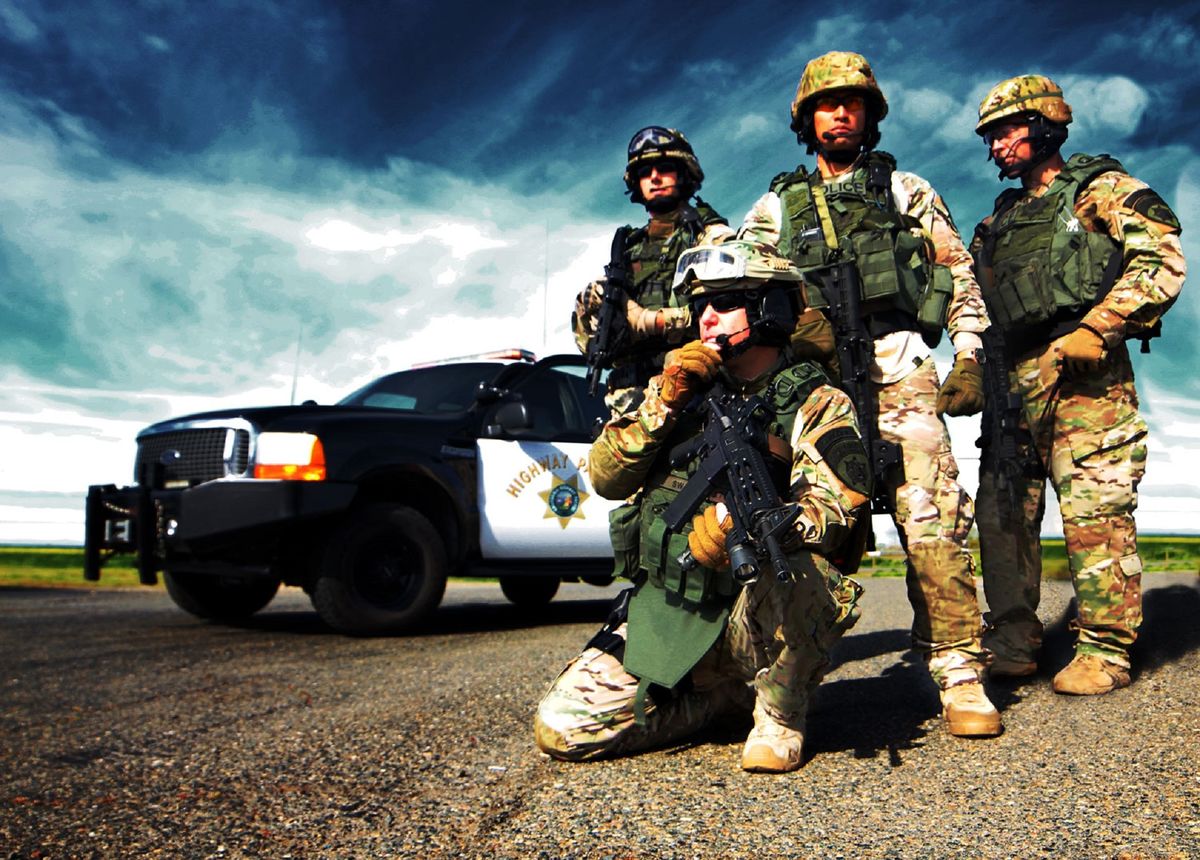
Real-World Impact on Law Enforcement Safety
The adoption of Kevlar in law enforcement has been a game-changer in terms of safety and survivability. Officers equipped with Kevlar vests have a significantly higher chance of surviving potentially fatal encounters. The material's ability to absorb and disperse the energy from a bullet or sharp object has saved countless lives.
The widespread use of Kevlar vests has not only provided protection but also instilled a sense of confidence among officers, knowing they have a reliable layer of defense.
Statistics from various law enforcement agencies illustrate the protective value of Kevlar. For instance, the National Institute of Justice (NIJ) reports a substantial decrease in fatalities among officers wearing body armor compared to those who do not. The following table presents a comparative analysis of officer survival rates with and without Kevlar armor:
Year | Officers Wearing Kevlar (%) | Officers Not Wearing Kevlar (%) |
---|---|---|
2018 | 95 | 70 |
2019 | 96 | 68 |
2020 | 97 | 65 |
These figures underscore the critical role that Kevlar has played in enhancing law enforcement safety. The material's evolution continues to focus on improving comfort and wearability, ensuring that officers are not only protected but also able to perform their duties without hindrance.
Kevlar in Motorsports: A Track Record
The integration of Kevlar into motorsports gear has been a game-changer for rider safety. Its high tensile strength and resistance to abrasion have made it an ideal material for racing suits and protective gear.
In the high-speed world of motorsports, crashes are an unfortunate reality. Kevlar's ability to dissipate energy and resist tearing has significantly reduced the severity of injuries for riders. The material's lightweight nature also contributes to greater comfort and maneuverability, which is crucial during long races.
The adoption of Kevlar in motorsports gear has not only enhanced safety but also improved performance by allowing riders to push the limits with confidence.
Motorcycle apparel has evolved to meet the diverse needs of riders. Versatile textile pants offer comfort and protection in various weather conditions with features like waterproofing, armor, and adjustability. Kevlar jeans provide style and durability, while leather pants prioritize safety and style. Each type of apparel brings its own set of benefits to the track, making Kevlar a versatile component in the motorsports safety arsenal.
Consumer Stories: Surviving Accidents with Kevlar Gear
The resilience of Kevlar gear in real-life scenarios is not just a testament to its material properties but also to the human stories of survival it underpins. Personal accounts from individuals who have experienced accidents while wearing Kevlar-enhanced protective gear provide compelling evidence of its life-saving potential.
- Motorcyclist Survival: A rider recounts a high-speed encounter with the pavement, crediting his Kevlar-reinforced jacket for preventing severe abrasions.
- Law Enforcement: Officers share experiences where Kevlar vests absorbed the impact of bullets, allowing them to return home safely to their families.
- Industrial Accidents: Workers in hazardous environments report instances where Kevlar gloves and aprons shielded them from potentially fatal cuts and punctures.
The narratives of those who have walked away from perilous situations unscathed offer a powerful endorsement for the widespread adoption of Kevlar in safety gear. These stories not only highlight the effectiveness of Kevlar but also underscore the importance of personal protective equipment in various high-risk professions and activities.
The data collected from these incidents also serve as a feedback loop for manufacturers, who continuously refine their products to enhance protection. The integration of consumer feedback into product development is crucial for the evolution of safety gear, ensuring that it meets the real-world demands of those it is designed to protect.
Consumer Perspectives and Market Trends
Public Perception of Kevlar-Enhanced Products
The public's perception of Kevlar-enhanced products has been largely shaped by their proven efficacy in providing protection and safety. The material's association with life-saving equipment in military and law enforcement contexts has bolstered its reputation among consumers. This esteem is reflected in the consumer market, where products boasting Kevlar reinforcement are often perceived as high-quality and reliable.
However, the perception of Kevlar is not without its nuances. While some consumers view Kevlar-enhanced gear as a necessary investment for personal safety, others may see it as an excessive precaution or a luxury. The market for these products is diverse, with varying levels of awareness and appreciation for the material's protective qualities.
The integration of Kevlar into consumer products has also sparked discussions about the balance between safety and comfort, as well as the cost implications of adopting such high-performance materials.
To better understand the public's view, consider the following points:
- The visibility of Kevlar in high-profile safety applications has elevated its status.
- Consumer trust in Kevlar is reinforced by positive testimonials and survival stories.
- The cost of Kevlar products can be a barrier for some, despite the potential safety benefits.
- Marketing efforts, such as those by Winx Wheels, play a significant role in shaping consumer perceptions.
Trends in Demand for High-Performance Protective Gear
The market for high-performance protective gear has seen a significant uptick in recent years, driven by heightened safety awareness and technological advancements. The demand transcends traditional sectors such as law enforcement and military, permeating into sports, construction, and even entertainment industries.
- Law Enforcement and Military: Continual investment in personnel safety has led to regular procurement cycles for updated gear.
- Sports: Athletes in extreme sports value the enhanced protection Kevlar offers against severe injuries.
- Construction: Workers seek gear that provides both safety and comfort during long hours on the job.
- Entertainment: Stunt professionals require gear that offers maximum protection without compromising on mobility.
The integration of Kevlar into various forms of personal protective equipment is not just a trend but a reflection of society's growing commitment to safety across all professional and recreational activities.
Consumer preferences have also shifted towards products that offer a balance between protection, comfort, and style. This has encouraged manufacturers to innovate and diversify their offerings, leading to a broader range of Kevlar-enhanced products in the market.
The Influence of Media on Safety Gear Popularity
The media's portrayal of safety gear, particularly in the realm of extreme sports and action-packed movies, has significantly shaped public perception. When celebrities and professional athletes are seen donning Kevlar-reinforced gear, it not only becomes a symbol of toughness but also a desirable fashion statement. This phenomenon has led to a surge in the popularity of such gear among consumers.
The marketing strategies employed by manufacturers often leverage this media influence. By associating their products with high-profile personalities and thrilling activities, they tap into the aspirational desires of the audience. The following list illustrates common media-related factors that contribute to the popularity of Kevlar-enhanced safety gear:
- Endorsements by influential figures
- Product placement in films and television
- Coverage of gear in action during sporting events
- Social media campaigns featuring real-life testimonials
The impact of media on safety gear popularity cannot be understated. It has the power to transform protective equipment from a mere necessity into a lifestyle choice. As such, the media plays a crucial role in both educating the public about the importance of safety and in driving the demand for Kevlar-based products.
Ethical Considerations and Social Responsibility
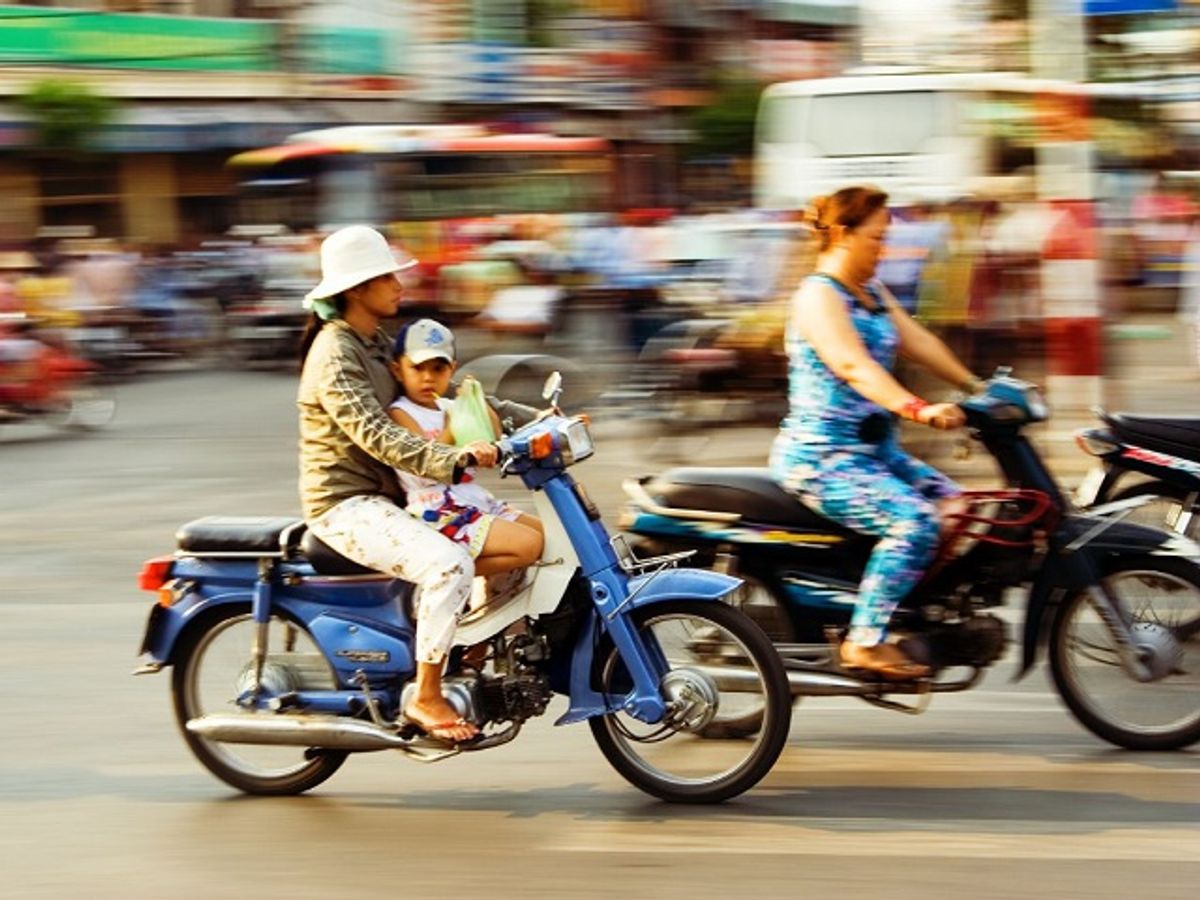
The Role of Manufacturers in Promoting Safety
Manufacturers play a pivotal role in promoting safety through the design and production of protective gear. They are responsible for ensuring that their products not only meet regulatory standards but also address the practical needs of consumers. The integration of advanced materials such as Kevlar into safety equipment is a testament to the industry's commitment to innovation and protection.
In the realm of motorcycle apparel, for example, manufacturers have successfully merged style with safety. The apparel is designed to be both aesthetically pleasing and functionally protective, often incorporating Kevlar to enhance durability and resistance to abrasions. This balance is crucial as trends in fashion increasingly prioritize functionality and safety, reflecting a growing consumer demand for gear that offers comprehensive protection without sacrificing style.
It is essential for manufacturers to continuously engage in research and development to refine the protective qualities of their products while maintaining comfort and wearability. This ongoing commitment to improvement is vital for the advancement of safety gear and the well-being of end-users.
To further illustrate the commitment to safety, manufacturers often provide educational resources and training programs. These initiatives are aimed at informing consumers about the proper use and maintenance of safety gear, which is critical for ensuring maximum protection.
Access to Protective Gear in Developing Regions
The disparity in access to protective gear such as motorcycle safety gear in developing regions is a significant concern. While affluent nations benefit from advanced materials and technologies, developing countries often face challenges in obtaining even basic protective equipment. This gap not only increases the risk of injuries but also exacerbates the socioeconomic divide.
- Lack of awareness about the importance of protective gear
- Economic barriers that prevent widespread adoption
- Limited availability of high-quality safety equipment
- Inadequate legal frameworks to enforce the use of protective gear
Ensuring equitable access to safety equipment like helmets, jackets, and gloves is crucial for reducing preventable injuries and fatalities on the road.
Efforts to improve access must consider the unique economic and infrastructural constraints of these regions. Collaborative initiatives between governments, non-profits, and manufacturers can play a pivotal role in making safety gear more accessible and affordable.
Environmental Impact of Kevlar Production and Disposal
The production and disposal of Kevlar, like many synthetic materials, raise environmental concerns that necessitate careful consideration. During the manufacturing process, the production of Kevlar requires significant energy input and the use of potentially hazardous chemicals, which can contribute to pollution if not managed properly.
The lifecycle of Kevlar products also presents challenges. While Kevlar's durability means a longer lifespan and less frequent replacement, the end-of-life disposal options are limited. Kevlar is not biodegradable, and recycling options are currently inadequate due to the complexity of the material.
Efforts to mitigate the environmental impact of Kevlar involve several strategies:
- Innovations in manufacturing: Reducing energy consumption and minimizing waste during production.
- Development of recycling techniques: Finding ways to reclaim and repurpose Kevlar fibers from used products.
- Material blends: Incorporating Kevlar with other materials to enhance recyclability.
The table below summarizes the key environmental considerations associated with Kevlar production and disposal:
Aspect | Concern | Mitigation Strategy |
---|---|---|
Energy Consumption | High energy input required | Innovations to reduce energy use |
Chemical Use | Potential pollution from hazardous chemicals | Safer chemical alternatives and containment |
Waste Generation | Non-biodegradable waste | Development of recycling and repurposing methods |
Lifecycle | Long product lifespan | Design for disassembly and recycling |
As the industry progresses, it is imperative to balance the undeniable benefits of Kevlar in safety applications with the responsibility to protect the environment.
Frequently Asked Questions
What is Kevlar and how was it discovered?
Kevlar is a synthetic fiber known for its high tensile strength and thermal stability. It was discovered by Stephanie Kwolek at DuPont in 1965 while searching for new materials to make lighter and stronger tires.
How is Kevlar used in military and law enforcement?
Kevlar is widely used in military and law enforcement for bulletproof vests, helmets, and other body armor components due to its ability to absorb and disperse impact energy from bullets and shrapnel.
Can civilians purchase Kevlar-based products?
Yes, civilians can purchase Kevlar-based products such as personal protective equipment, including bulletproof vests, motorcycle gear, and cut-resistant gloves, subject to local laws and regulations.
What makes Kevlar suitable for personal protective equipment?
Kevlar's high tensile strength, durability, and resistance to thermal degradation make it an ideal material for personal protective equipment, providing protection without excessive weight or bulk.
How has Kevlar improved biker safety gear?
Kevlar has been integrated into motorcycle apparel to enhance protection against abrasions, cuts, and impacts. It is particularly effective in high-impact areas and helps reduce the severity of road rash injuries.
What manufacturing processes are involved in producing Kevlar fabrics?
Kevlar fabrics are produced using specialized weaving techniques that align the fibers to maximize their strength. Quality control is crucial to ensure the protective properties of the final product.
Are there any standards for testing Kevlar-based protective gear?
Yes, there are national and international standards that outline testing protocols for Kevlar-based protective gear. These standards ensure that products meet specific safety requirements before reaching the market.
What are some potential future applications of Kevlar?
Future applications of Kevlar may extend beyond protective clothing to areas such as construction, aerospace, and automotive industries, where its strength and durability can be leveraged in new ways.